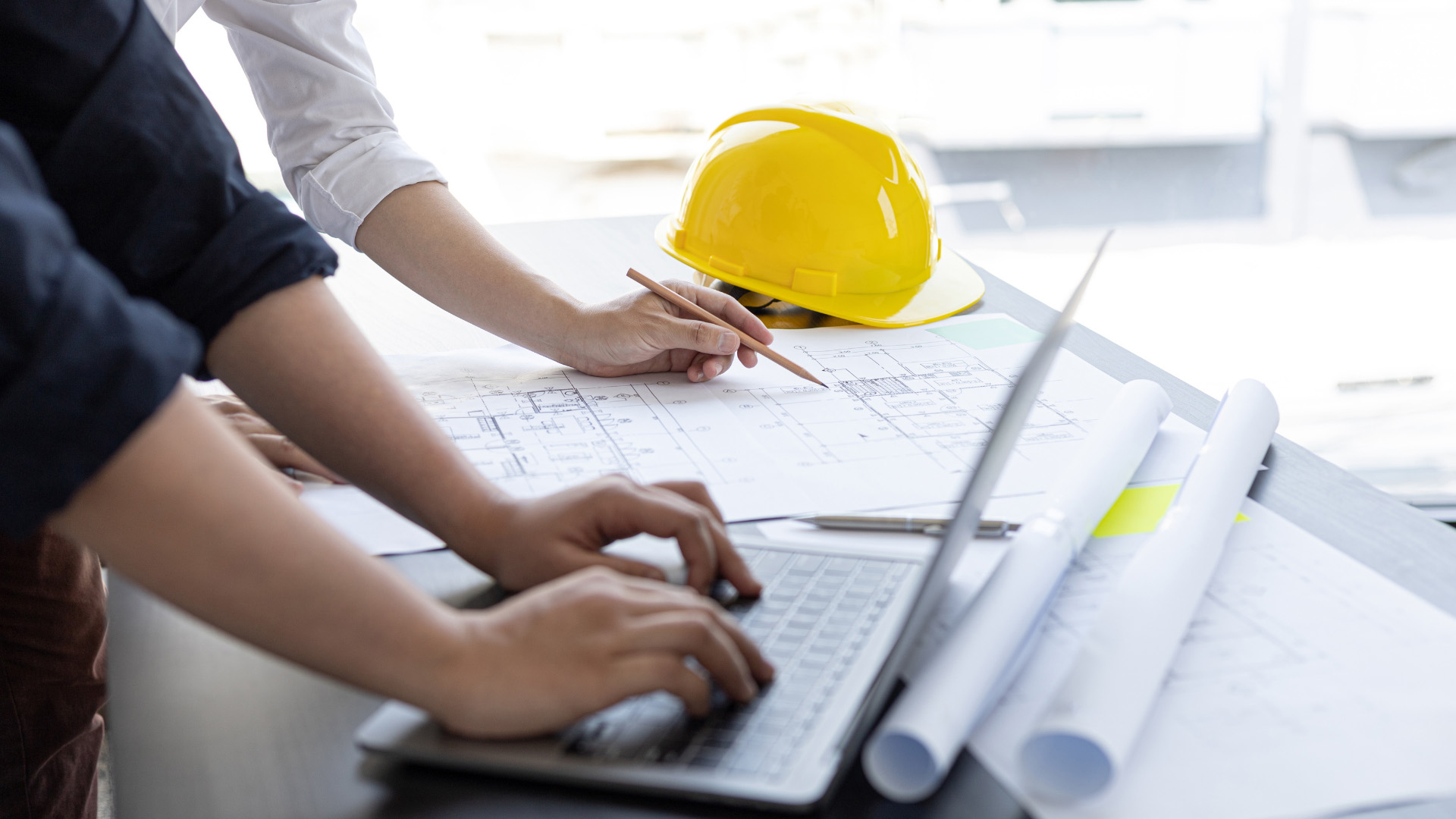
4 reasons to choose a local automation solutions provider
Lithuanian businesses modernising their production processes take into account the geographical location of their suppliers when looking for ways to improve efficiency. In recent years, there has been a tendency among manufacturing companies to procure their main machining tools from abroad and to implement the necessary automation solutions by choosing local suppliers. There are a number of reasons for this practice, ranging from the desire to save money to the need to meet demand more smoothly.
Designing for individual needs
Companies choose to work with a local supplier of manufacturing automation services primarily because of the possibility of getting customised solutions. Local suppliers have a much better understanding of the needs of companies in their area and, by looking into the unique requirements of the company, can more easily design solutions to meet specific requirements.
Flexibility and seamless communication
Before a supplier undertakes engineering planning, all technical issues are discussed: the need for automation is clarified, limiting factors are discussed in relation to existing equipment and other details. Working with a local supplier makes the whole process smoother – face-to-face communication, corrections, immediate feedback, and, if necessary, the supplier’s representatives can come to the customer’s premises to resolve the technical planning issues faster. Finally, a clear and effective communication between supplier and customer in this area is the key to a successful project.
Better price and significantly lower delivery costs
By working with trusted local service providers, manufacturers save money as domestic equipment supply companies can offer lower prices due to the lower overheads that are typical of foreign suppliers. Also, buying automated equipment from as close to the factory as possible can reduce or avoid shipping costs. It also ensures that the equipment arrives quickly and undamaged.
Rapid response and assistance
Equipment downtime can have a significant impact on a business. Waiting for assistance from an overseas supplier can mean higher costs and sometimes even losses. Meanwhile, local service providers are ready to react quickly to unexpected customer situations by sending specialists to provide support services or delivering spare parts. Timely troubleshooting significantly reduces downtime.